Upgraded Services for Life Sciences in Amsterdam
We are excited to announce our upgraded services via our pre-conditioning room in Amsterdam!
Firstly, recognising the Netherlands as a key hub for Life Sciences in Europe, our team upgraded our existing pre-conditioning facilities to meet rising demand and enhance our temperature-controlled services.
The facility has been temperature mapped according to GDP guidelines and is fully equipped with various refrigeration units, thermal boxes, dry shippers and high-end data loggers. Our upgraded services increased out storage capacity for shipments, thus our team is able to support a higher volume & frequency of shipping requests. Our additional monitoring solutions provide all partners with high shipment visibility.
We are also proud to announce that our Amsterdam office is GDP and ISO certified. Our team ensures quality driven solutions through our validated equipment, trained professionals and global operating procedures. Royale International offers a one-stop solution that mitigates biologistics risks and ensures successful deliveries.
Our Regional Head of Life Science – Europe, Søren Knudsen, is available to address biologistics queries within the region. Our experts also offer logistics solutions that cater to various life science products.
Feel free to reach out by email soren.knudsen@royaleinternational.com or contact him at +44 7717 846 890.
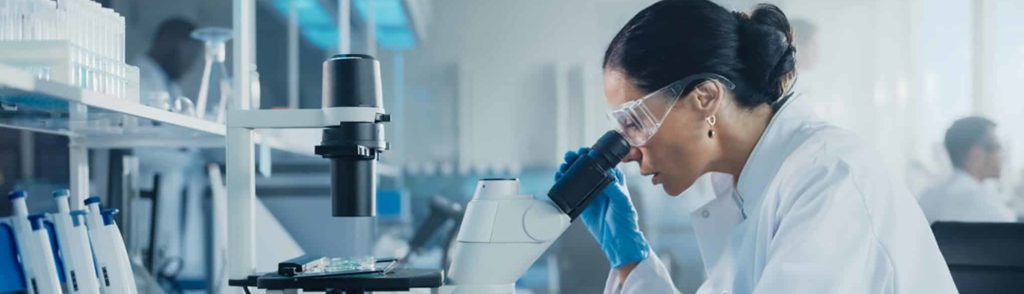
Upgraded Services in action
How Royale’s upgraded services enhance biologistics capabilities? Let’s review with the case study below:
“A stem cell donor was found in Turkey. Their cells needed to be shipped to Israel within 72 hours before it lost its viability. A medical courier in Turkey was found and dispatched to Germany for a connecting flight to Israel. However, bad weather arrangements led to a delayed flight and made it impossible for the specimen to be delivered via the initial route. Another medical courier was dispatched from Israel on a chartered flight with all the prepared documents they needed to enter Turkey and personally pick up the specimen. The courier returned to Israel and dropped off the shipment at the hospital for use.”
The top-tier and unified training of both couriers involved showed flexibility when delays took place. It was the initial courier’s transparency in communicating delays that allowed our industry experts to re-route the shipment. Finally, it was the adaptability and experience of our couriers, that made them prepare their documents (especially during the pandemic period) and avoid time-costing errors for the shipment.